Pin Fracture - Corrosion Fatigue |
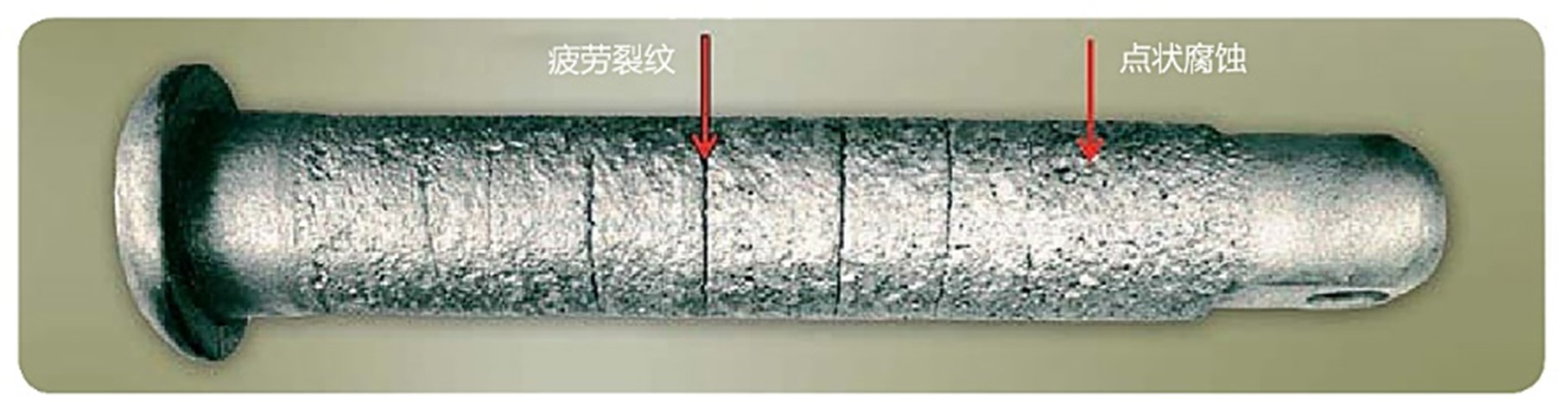 |
When load is applied to the chain, it accumulates between the "backside" of the pin and the inner walls of the link or bushing. If the chain pin operates in conditions with water, acid-base compounds, or situations where water generates acid, and it lacks protection, the exposed areas of the pin are susceptible to corrosion and pitting. Like any structural component, the chain pin slightly bends under load. In this case, the back surface of the pin is stretched or under tension, and if the pin has already been corroded, each pit becomes a stress concentration point.
|
Pin Wear - Abrasion, Insufficient Lubrication, or Failure |
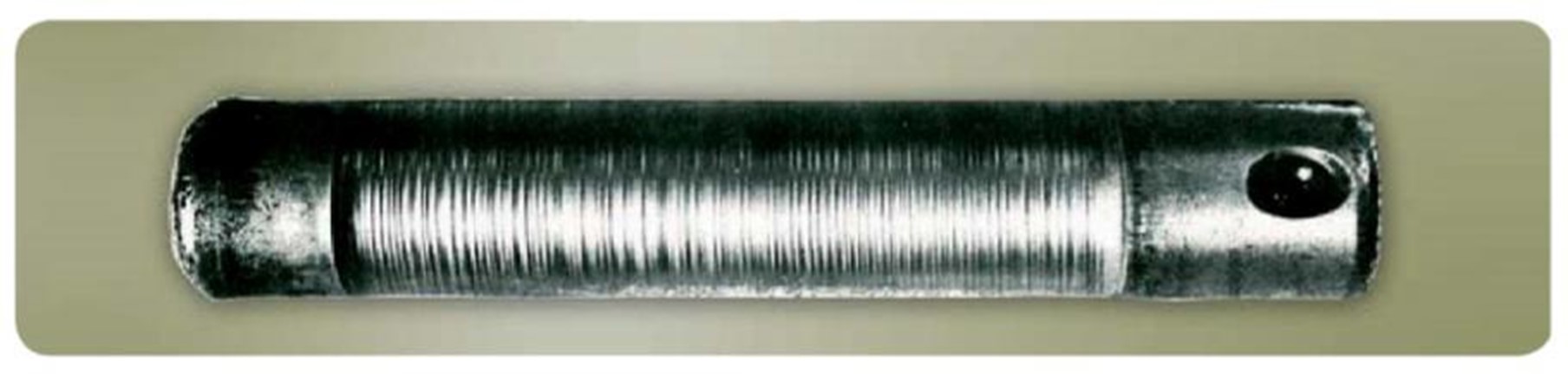 |
The presence of abrasive materials or an ineffective oil film between bearing surfaces accelerates wear. The pin shown here works in a power transmission chain exposed to sand and dirt. These abrasive materials penetrate the links, causing the pin to wear quickly, significantly reducing the chain's lifespan.
|
Pin Scuffing - Insufficient Oil Film Between Bearing Surfaces |
 |
If the oil film is insufficient to support the load or lubrication ceases for any reason, the chain pin will become roughened. Naturally, the intensity of wear depends on the degree and duration of metal-to-metal contact. Even a short period of operation under unusually severe load conditions or at very high speeds can cause early or moderate wear. This type of scuffing may not significantly affect the chain's lifespan, and if preventive measures are taken in time, the situation may not worsen. More intense wear can be observed when heavy-duty chains operate at very high or very low speeds. At high speeds, pin wear may occur because the time between load cycles is insufficient to form an adequate oil film. At very low speeds, high bearing pressure may squeeze out the lubricant, and continuous heavy loads may prevent the lubricant from reforming between the bearing surfaces. Certain variations in load and speed typically allow the lubricant to function effectively, reducing the tendency for pin wear.
|
Pin Shearing - Sudden Severe Overload |
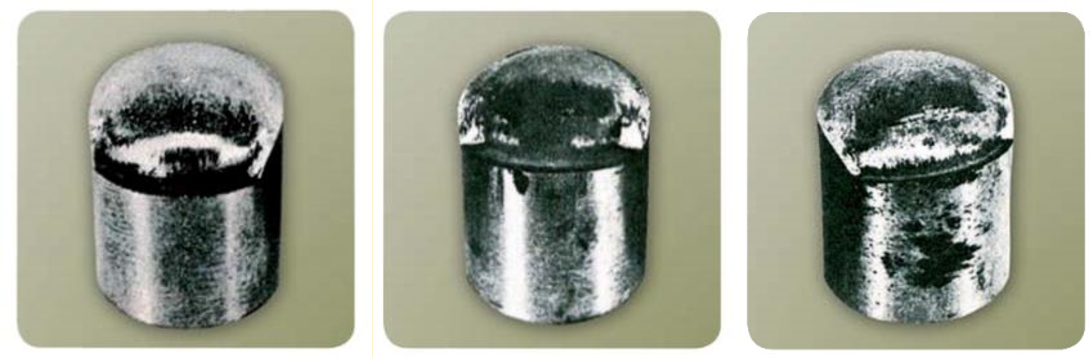 |
If pin separation occurs, it can usually be traced back to sudden, abnormal severe overload. An unexpected blockage is a common cause. As shown in the illustration, a severe impact load was applied to an already heavily loaded chain, causing the pin to shear. Pin shearing is characterized by a round, relatively smooth cross-section. Since pin shearing can be traced back to abnormal load conditions, the cause can usually be identified and preventive measures taken.
|
|
 |
Pin bending usually results from a sudden load applied strong enough to cause permanent deformation but insufficient to cause pin shearing. This occurs when the drive chain operates beyond its designed load capacity. This phenomenon is observable in heavy-duty conveyor chains, where a sudden increase in impact load exceeds the chain's normal working capacity. Corrective measures are typically taken to reduce the severity or likelihood of overload.
|
Pin and Bushing Erosion - Water, Abrasive, and Corrosive Materials |
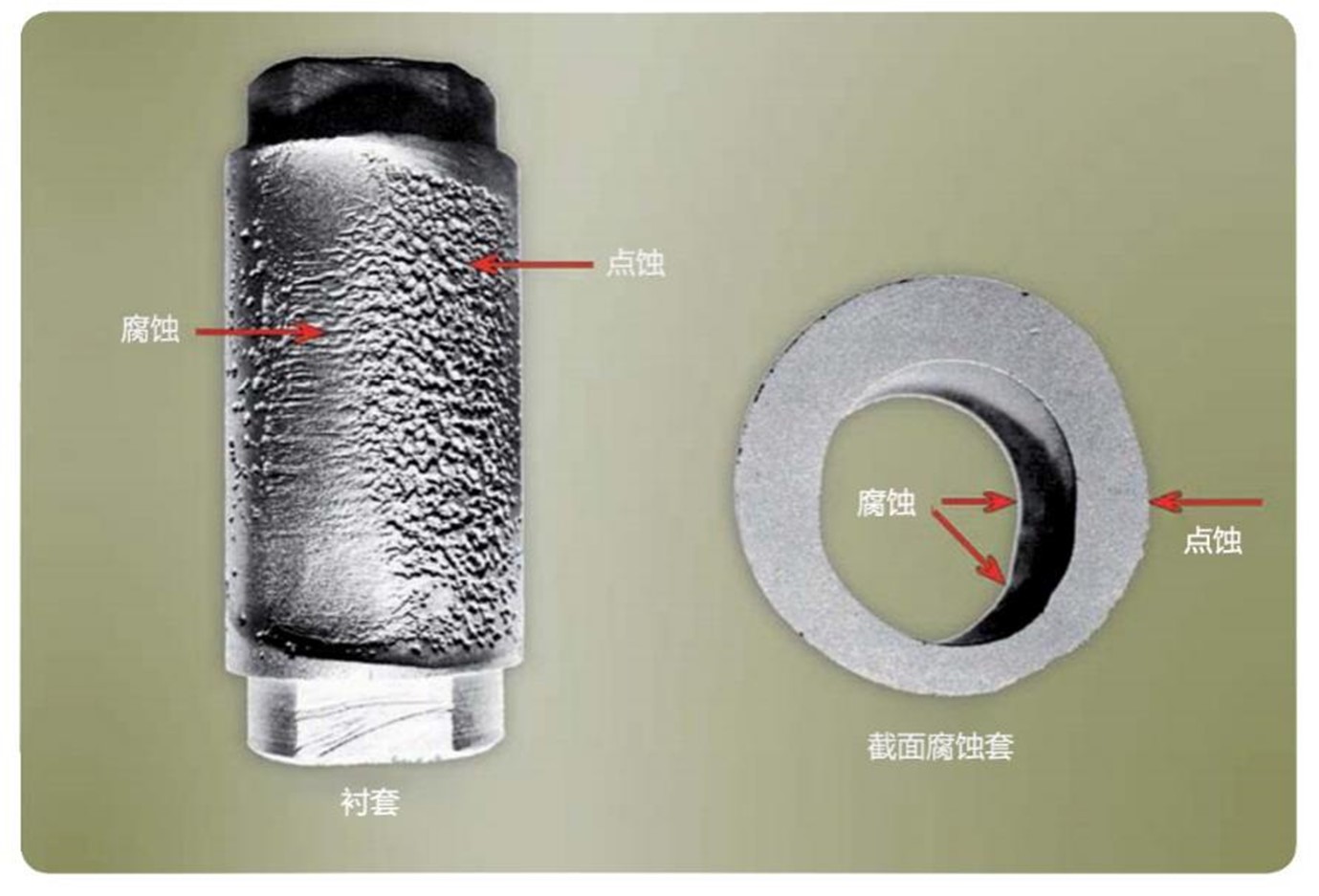 |
Chain link bearing surfaces may corrode when the chain operates in the presence of water, abrasive, and corrosive materials. The extent and rate of erosion depend on the severity of the conditions. Erosion is a continuous process where abrasive contaminants and water combine to wash away steel particles from the bearing surface, gradually reducing the cross-sectional area of the pin and bushing.
|
Joint Seizing - Corrosion, Wear, or Filling of Joints |
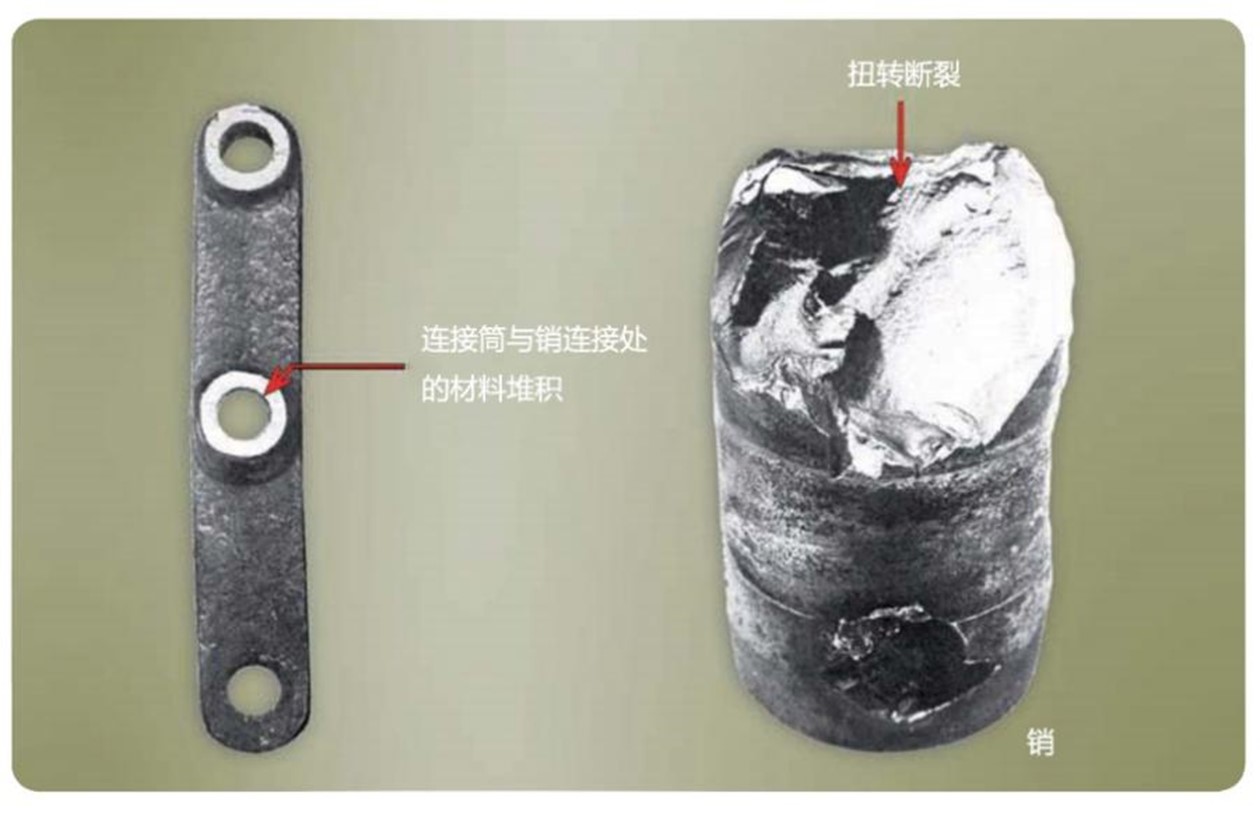 |
If bearing surfaces are severely corroded or worn, or gaps between joint parts are filled with materials prone to hardening, the link joints are susceptible to seizing or sticking. When the chain articulates on the sprocket, the joint parts may loosen. In the case of rigid joint engagement, pin torsion fracture or side plate pitch hole tearing may occur. Chain joints may also seize or stick due to wear if the chain operates beyond its speed limits. A protective coating can be used to prevent rust and potential seizing when the chain is subject to intermittent operation or extended periods of inactivity.
|
Side Plate Fatigue at Pitch Points - Cyclic Loading |
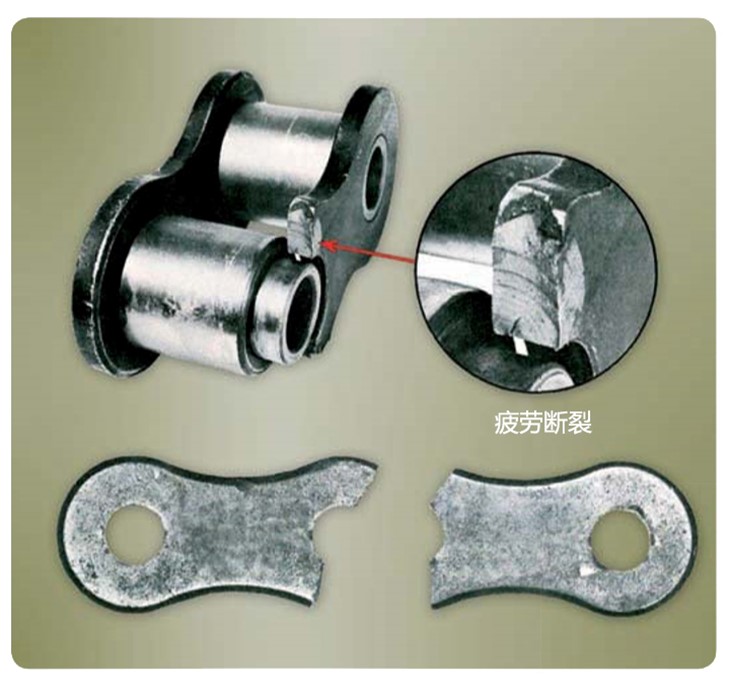 |
Side plate fatigue failure begins with very small cracks at the edges of pitch holes. Repeated load cycles gradually propagate the cracks outward until the side plate is sufficiently weakened to allow complete fracture. Fatigue failure is characterized by a series of concentric curves in an area with a brittle fracture appearance. A thorough analysis of all operating conditions is usually required to find an effective solution.
|
Roller Fatigue - Corrosion, Wear, or Filling of Joints |
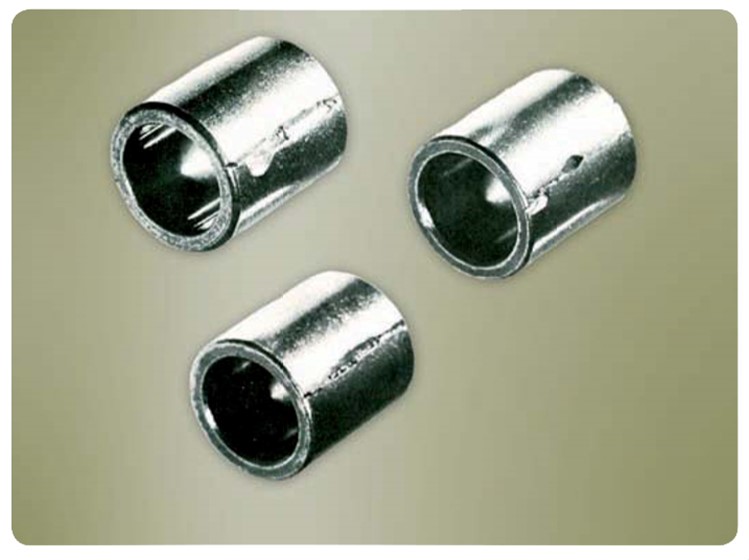 |
Some impact occurs when the sprocket contacts the sprocket teeth. If the operating conditions involve heavy loads and high speeds, the impact from tooth engagement can be severe, generating enough force to cause high stress on the roller surface. Repeated impacts can lead to fatigue cracks. Eventually, the roller may fracture due to metal fatigue. Reducing load and speed often overcomes roller fatigue.
|
Crushed Rollers or Bushings Due to High Load |
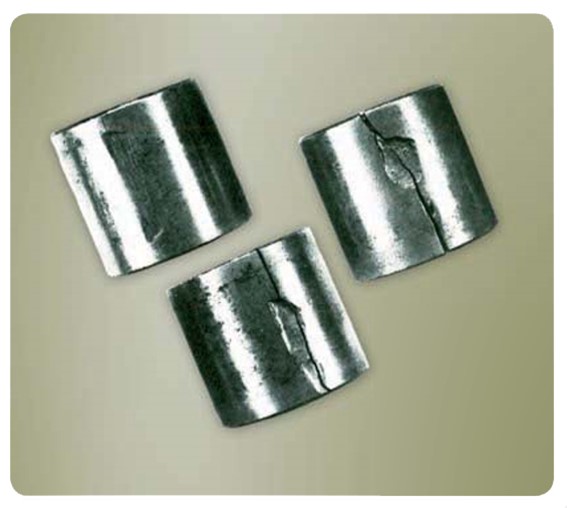 |
Due to pitch elongation, severely worn chains may no longer seat properly on their sprockets. Some rollers (or bushings) may contact the tips of the sprocket teeth, applying enough load to crush the rollers or bushings. When this type of engagement is observed, the chain should be replaced to prevent excessive sprocket damage. Severe overloading from unexpected jamming can also crush rollers or bushings. In such cases, corrective measures are usually taken to prevent the incident from recurring.
|
Link Wear - Sliding Between Traction Wheel and Chain |
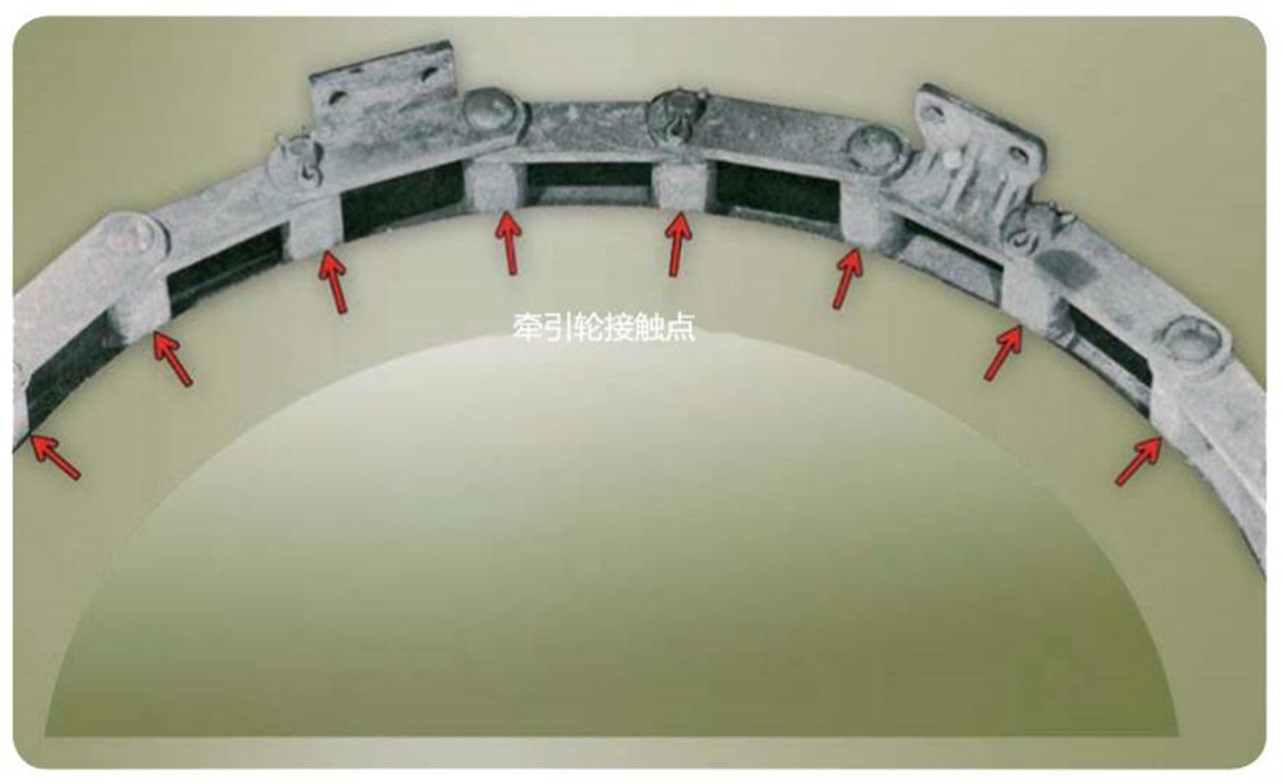 |
For bucket elevators and other applications, lower-cost traction wheels are often used instead of sprockets. Adequate traction between the chain and drive wheel is essential for efficient operation. The link shown in the illustration is used in a bucket elevator handling hard abrasives. The severe wear exhibited is caused by sliding during peak load periods. In this case, the traction was insufficient to effectively drive the chain.
|
Abnormal Chain, Sprocket, or Track Wear - Misalignment |
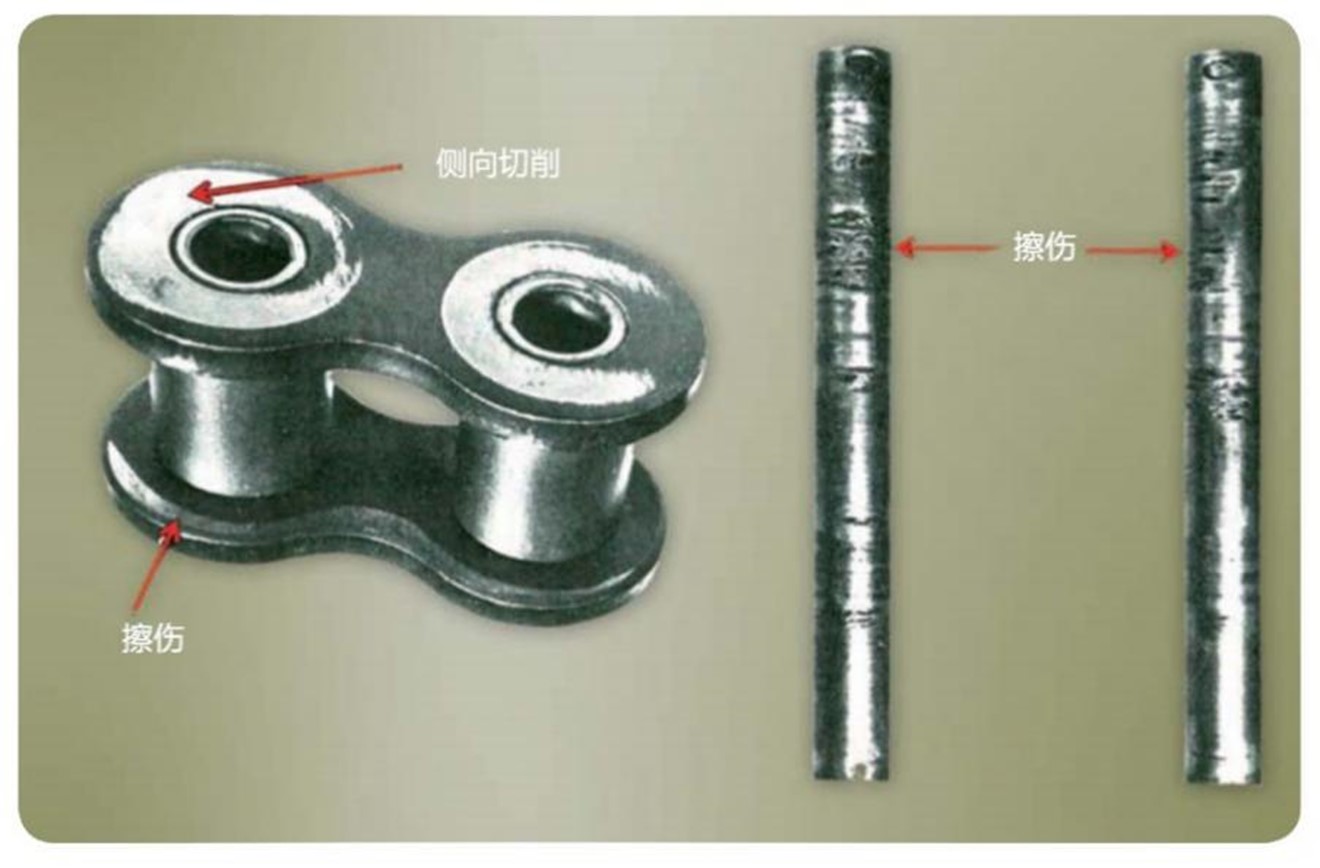 |
Unusual wear patterns on chains typically indicate misalignment, which can lead to severe chain damage. The most common types of misalignment are: In cases of misalignment, one side of the chain is overloaded, and the chain is forced to twist or distort as it moves from one sprocket to another. Uneven chain loading can lead to pin wear, side plate failure, or rapid wear. The best preventive measure against chain damage from misalignment is to regularly inspect the drive and conveyor system.
|
Chain Elongation (or Stretching) - Tensile Overload |
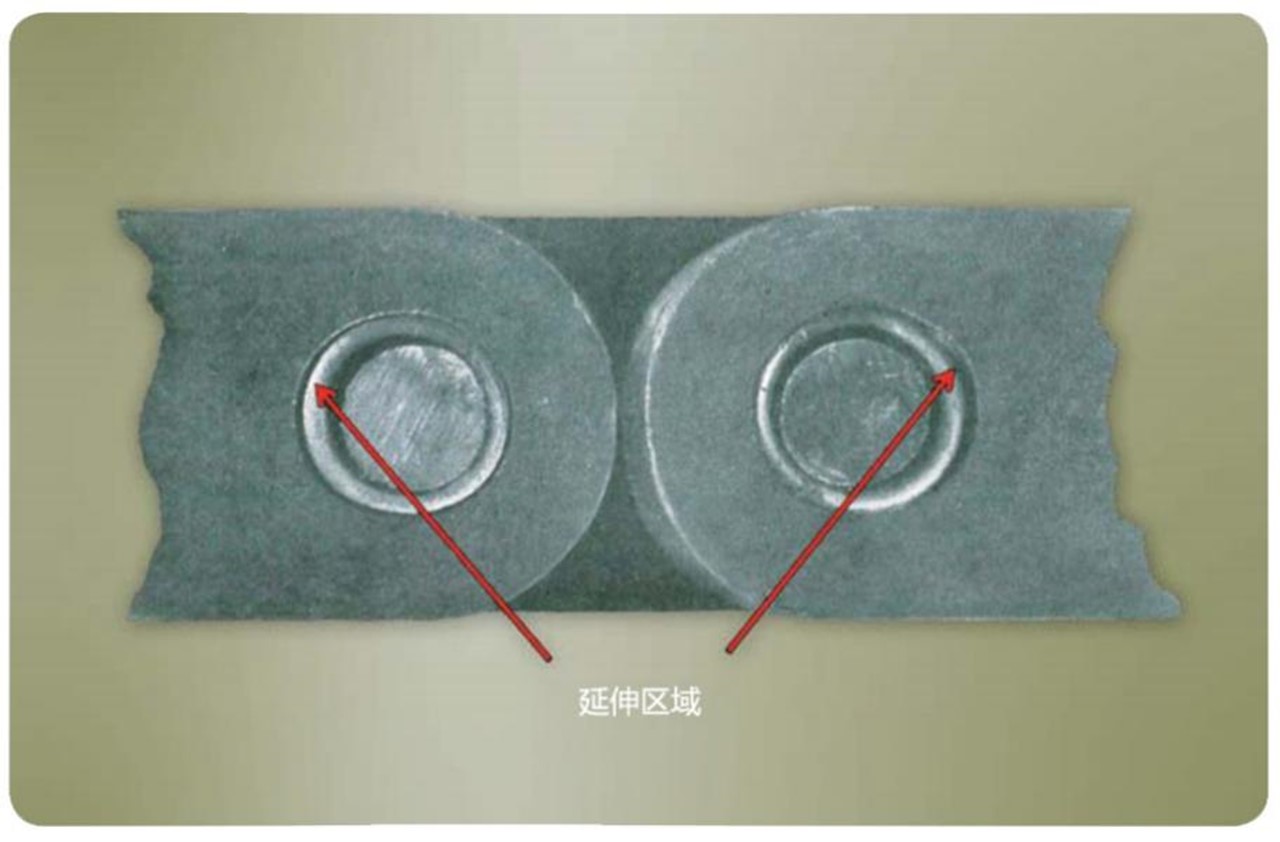 |
This type of elongation involves plastic deformation, where the side plate material is loaded beyond its yield point but not its ultimate strength. As a result, the side plates permanently stretch but do not fracture. If pitch elongation is severe, the chain will no longer mesh properly with the sprockets. Tensile overload leading to chain elongation can occur when equipment is forced to operate beyond its design capacity, due to unexpected blockages, or for similar reasons. Corrective measures are typically taken to prevent further overload. Sometimes, shock-absorbing devices can be used to avoid transmitting overload to the chain.
|