High Temperature Chain Oil in Rock Wool Production
In the rock wool production process, to facilitate the polymerization of resin in the mats, hot air at 300-350℃ is blown into the curing furnace’s heating zone. As a result, the chains in the curing furnace are exposed to a high-temperature environment of 260-280℃ for extended periods. However, most chain oils tend to carbonize and form polymer residues and dry powdery substances at such temperatures, hindering the chain’s effective operation and leading to issues like chain jamming, elongation, and even breakage.
1.Characteristics of Rock Wool
Rock wool is a type of mineral wool, which is an inorganic fiber material. Mineral wool is produced by melting various mineral raw materials, forming fibers, and treating them with organic or inorganic reagents to create a wool-like fiber. Rock wool is a commonly used insulation material and is a type of mineral wool.
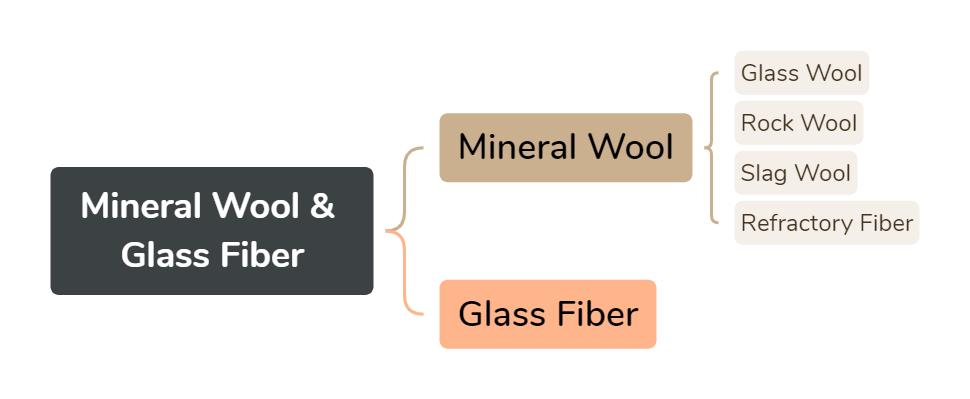
Mineral wool is closely related to glass fiber and is a different type of inorganic fiber material. Based on the source of raw materials, mineral wool can generally be divided into:
- Glass wool: Made primarily from silicate minerals that form glass.
- Rock wool: Made primarily from basalt, diabase, etc.
- Slag wool: Made primarily from blast furnace slag, phosphorus slag, etc.
- Refractory materials: Made primarily from high-silicon and high-aluminum content ores, such as hard clay, kyanite, silica sand, alumina, etc.
2.Curing Furnace Temperature and Chain Oil Selection
In rock wool production lines, the curing furnace's hot air temperature typically ranges from 300-350℃. Conventional chain oils tend to evaporate quickly at this temperature, and if their adhesion is poor, they may drip, causing product and environmental contamination.
When producing rock wool boards, the customer had been using inexpensive conventional high-temperature chain oils, which evaporate quickly, leading to high consumption. One of the customer's old rock wool production lines had been poorly lubricated and maintained for an extended period, causing the chains to emit a "squeaking" noise during operation. The viscosity of conventional chain oils at 40℃ is around 320 cSt. However, due to the large size of the sprockets and chains in the curing furnace, a higher viscosity oil is needed to prevent dripping while also ensuring good penetration.
3.Production and Lubrication Process
Rock Wool Board Production Process
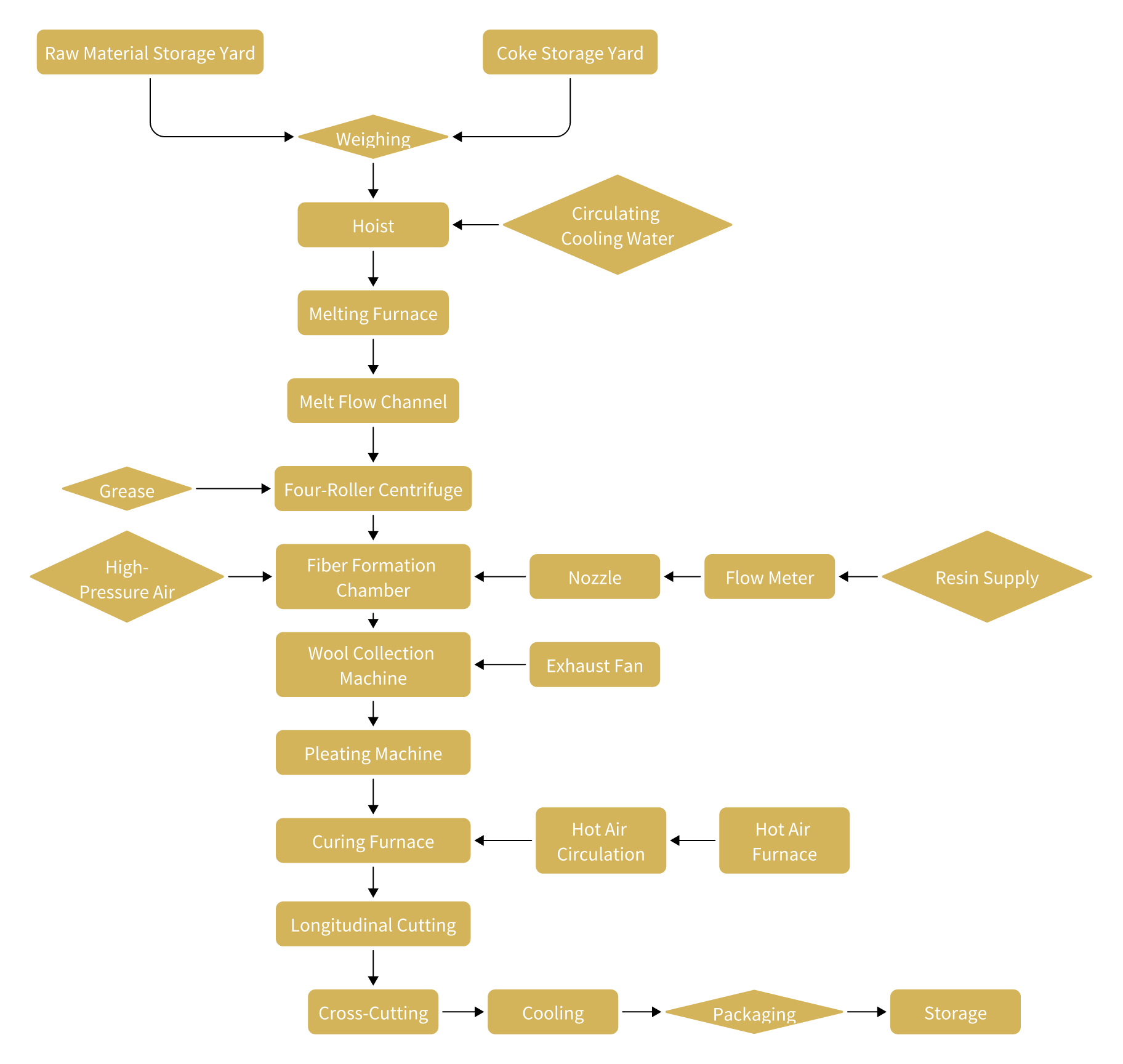
- Application of High Temperature Chain Oil
The chain oil is used in the curing furnace process. After the resin mat exits the settling chamber, it is pre-pressed by pressure rollers and then enters the curing furnace for heat treatment, where the resin is dehydrated and cured, forming a product with a fixed structure and shape. This is a critical step in the production of slag wool and rock wool insulation boards. The hot air blower sends hot air at 300-350℃ into the curing furnace's heating zone, allowing it to pass through the wool layer to evaporate moisture and cure the resin.
- Chain Lubrication
The chains should be lubricated at designated points before entering the curing furnace by brushing or oil cup dripping.
Curing Furnace Outlet |
Chains Emit Noise |
Rock Wool Products |
---|---|---|
|
|
|
4.Issues Identified
- Conventional high-temperature chain oil cannot withstand temperatures of 260-300℃. It quickly evaporates in the curing furnace, failing to provide effective lubrication.
- The high ambient temperature makes manual brushing difficult, hindering timely lubrication.
- The chains have already started making noise due to poor or lack of lubrication.
- Carbon buildup on the chains has affected their operational efficiency and lifespan.
5.Solution
Given that the actual temperature in the customer's curing furnace is consistently between 260℃ and 280℃, it is recommended to use a high-temperature-resistant synthetic oil. Additionally, since the rock wool production line's chains and sprockets are large, the selected high-temperature chain oil needs to have sufficient adhesion and penetration. Strong adhesion prevents the oil from dripping, avoiding environmental pollution and waste, while good penetration ensures that the base oil reaches the lubrication points, preventing direct contact between rollers and sleeves, and between pins and sleeves, thereby achieving effective lubrication.
- Coomcool Chain RWL 900: This product uses synthetic base oil, featuring extremely low evaporation loss and minimal high-temperature carbon buildup. It is specifically designed for lubrication in rock wool production line curing furnaces.
- Manual brushing often results in uneven or untimely application. The company's engineers have designed a special aluminum-shell oil cup that effectively addresses the impact of high temperatures on lubrication equipment. After two years of use, the chains have shown no abnormalities, proving that this product can fully meet the lubrication needs of chains in high-temperature environments.